Reskilling: Key to Success in Industrial Robotics and Industry 4.0
JD
Understanding the Need for Reskilling in Industrial Robotics
The rise of Industry 4.0 marks a significant shift in how industries operate, driven by advancements in digital technology and automation. At the heart of this transformation is industrial robotics, which is revolutionizing production processes. However, for businesses to fully harness the potential of these technologies, a new approach to workforce development is necessary. This is where reskilling becomes crucial.
Reskilling involves training employees in new skills that align with the demands of modern technology. As industrial robotics continue to evolve, the need for workers who can operate, manage, and innovate within these systems becomes more pressing. Companies that invest in reskilling programs are better positioned to thrive in the fast-paced world of Industry 4.0.
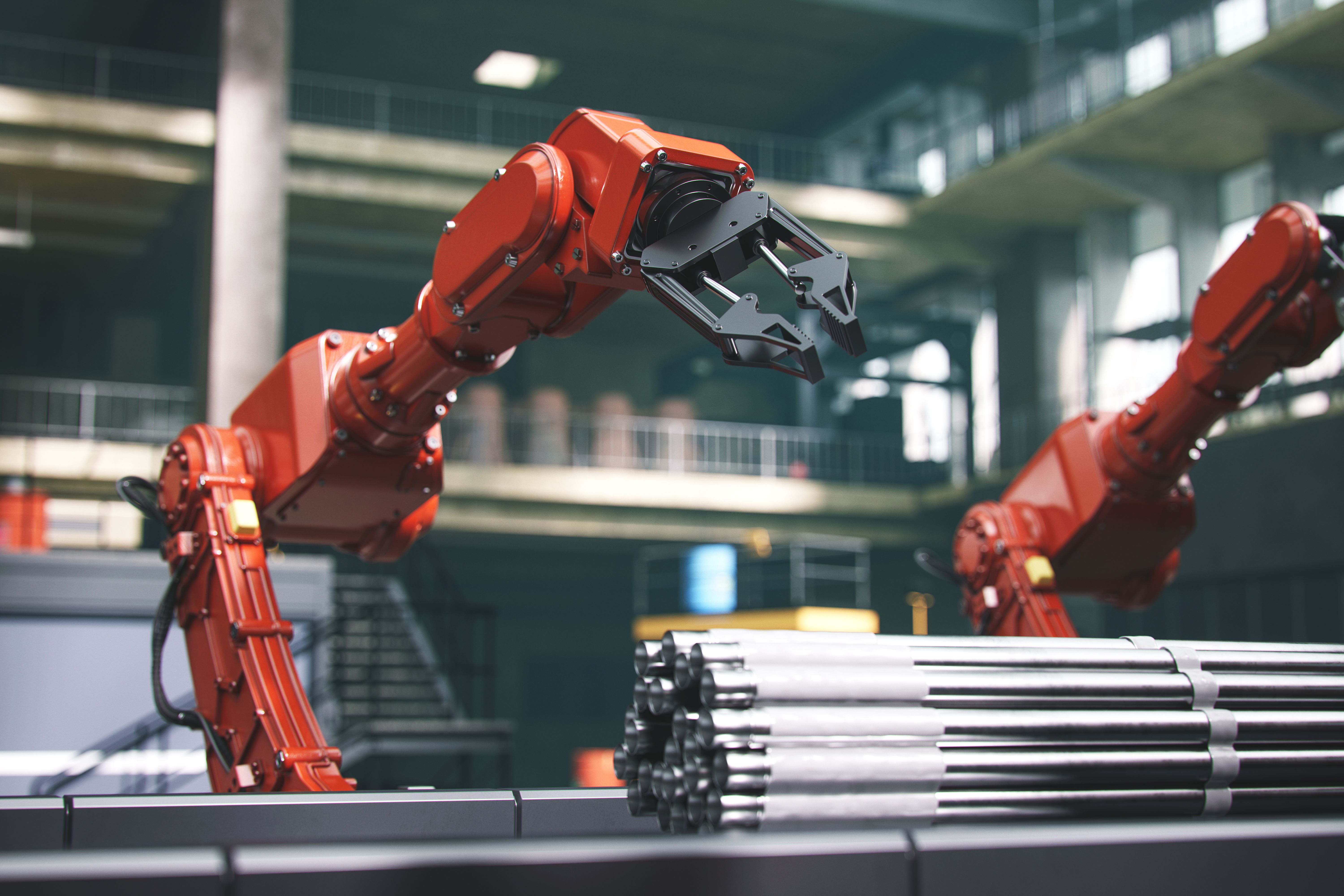
The Benefits of Reskilling for Organizations
Investing in reskilling offers several benefits for organizations looking to integrate industrial robotics into their operations. Firstly, it ensures that the workforce is equipped with the necessary skills to work alongside advanced machinery, minimizing disruptions and maximizing productivity. This creates a more agile and adaptable workforce capable of meeting the challenges posed by technological advancements.
Additionally, reskilling can lead to increased employee satisfaction and retention. Workers who receive training and development opportunities feel valued and are more likely to stay with the company. This reduces turnover rates and fosters a culture of continuous learning and innovation.
Enhanced Operational Efficiency
By reskilling employees, companies can improve their operational efficiency. Employees with updated skills can quickly adapt to new technologies and processes, reducing downtime and increasing overall output. This agility is particularly important in industries where rapid changes are the norm.
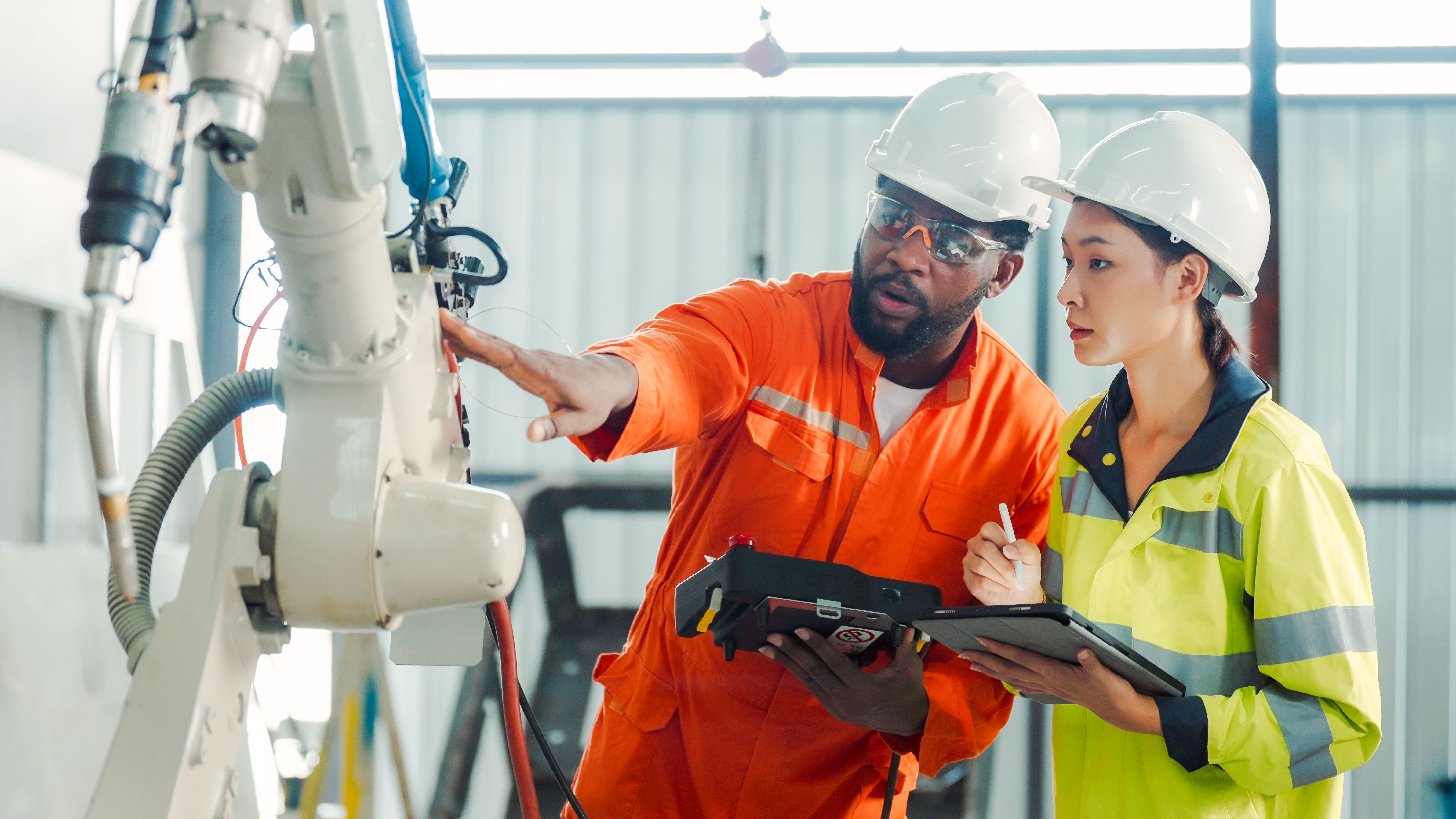
Navigating Challenges in Reskilling
While the benefits of reskilling are clear, implementing effective programs can be challenging. One of the main obstacles is identifying the specific skills that need to be developed. This requires a thorough analysis of current operations and future needs. Collaborating with technology providers and educational institutions can help bridge this gap.
Moreover, companies must overcome resistance to change from employees accustomed to traditional ways of working. Communicating the long-term benefits and providing support throughout the transition can ease these concerns.
Strategies for Successful Reskilling
A successful reskilling program involves several key strategies:
- Assessment: Conducting a skills assessment to identify gaps and areas for development.
- Collaboration: Partnering with educational institutions and technology providers for tailored training programs.
- Continuous Learning: Encouraging a culture of ongoing education and skills development.
- Incentives: Offering incentives such as career advancement opportunities for employees who participate in reskilling programs.
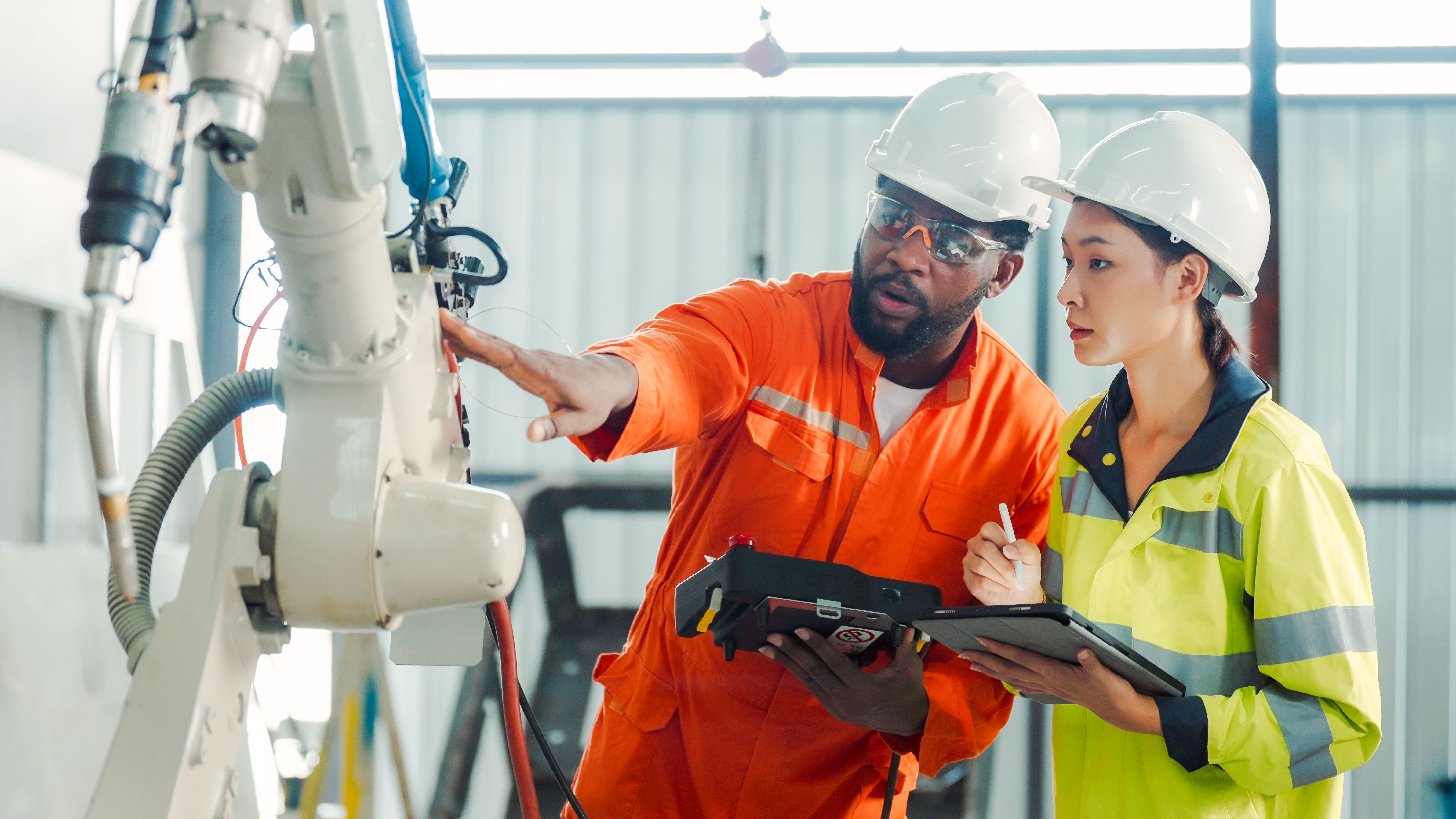
The Future of Work in Industry 4.0
The integration of industrial robotics into various sectors signifies a new era for the workforce. As Industry 4.0 continues to shape the future of work, the importance of reskilling cannot be overstated. It empowers employees to stay relevant in their roles while enabling companies to maintain competitiveness in an ever-evolving market.
Ultimately, reskilling is not just about adapting to change but embracing it as an opportunity for growth and innovation. By prioritizing workforce development, companies can ensure they are not only participants in Industry 4.0 but leaders in the next industrial revolution.